Commutator
After several hours of operation, the commutator surface under the brush should take on a darker bronze color. This is due to self-generated film caused by normal commutation. This coloration should be even, without blotches or black areas. A shiny copper color or black streaks in the brush tracks are signs of improper commutation or contamination by a foreign material. Contact us for assistance in correcting these problems.
If the commutator becomes rough and burned, or becomes black. It should be cleaned of dirt and carbon particles. This can be done by wiping it with a dry, lint-free cloth. Also vacuuming or blowing out the motor with a dry air supply is suitable cleaning methods. Do not use solvents or cleaning solutions on the commutator. To remove spots or contamination the will not wipe off, wrap a strip of coarse (60# grit) sandpaper around the commutator. Then rotate the armature back and forth by hand. Do not use emery cloth as this contains electrically conductive materials.
Another method of commutator resurfacing is to use a commercially available commutator dressing stone. This should only be done by trained and experienced people. This stone should be taped or attached to the end of a stick made of electrically insulated material. The motor should be run at about half speed and the stone applied lightly to eh commutator surface. This operation must be done with no load on the motor. Be careful of applied voltage hazards.
Humidity and brush wear
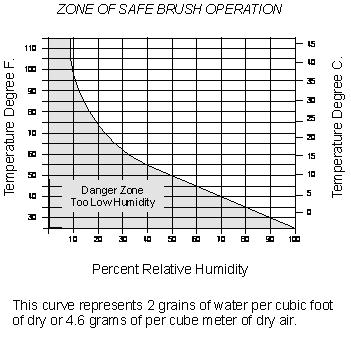
Turning the Commutator
After commutator turning, check it run-out with the bearings on V block. For all commutators, maximum run-out is .002”. New and minimum commutator diameters are in the cart that follows. |
|

NOTE:
- The above diameters are approximate.
- They are for standard design and speed motors. High speed motors require.
- Larger minimum bar diameters.
The surface of the commutator should be smooth and round. This can be checked while the motor is running at low speed. Press lightly on one brush with an insulated stick. Do not use a lead pencil as this contains electrically conductive graphite. If you feel movement of the brush, it suggests a worn or uneven commutator. The armature must be removed from the motor and the commutator turned by a qualified repair shop.
Rapid Commutator Wear
Light electrical loads and contamination are the usual causes of rapid commutator wear.
Light loading may require the removal of some brushes on motors with multiple brushes per pole. Sometimes we substitute a low current density brush grade. There are also brushes available that have a mild polishing action. These prevent certain chemicals, especially chlorine and silicone, from attacking the commutator. Brushes are available for plastic extruder applications where PVC is present. Usually, you don’t have to change the design or grade of the brushed on new motors unless special operating conditions exist.
DO NOT CHANGE BRUSH GRADES OR THE NUMBER OF BRUSHES PER POLE. DOING SO MAY VOID THE WARRANTY AND MAKE THE MOTOR UNSAFE. CONTACT YOUR LOCAL AGENT DISTRICT OFFICE OR AN AUTHORIZED SERVICE CENTER FOR TECHNICAL ASSISTANCE.
Commutator undercutting
Check the commutator mica between bars for an under-cut depth of 1/64” minimum, 3/64” maximum. The grooves of the under-cut are to be free of mica and chips.
|